External design and internal design changes of automotive wiring harness
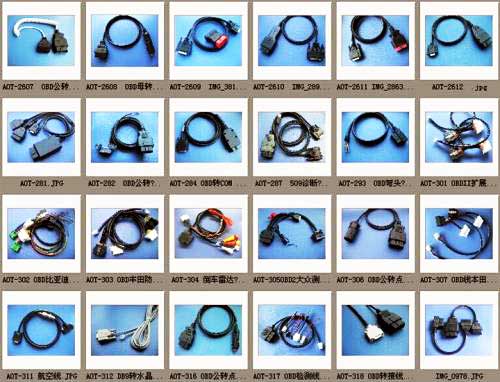
The wiring harness industry is a very flexible industry in the field of auto parts, and the design changes involved are usually very frequent. For example: the increase or decrease of the electrical configuration of the vehicle in the automobile factory, the design change of the installation position of the electrical appliance, the design change of the electrical terminal connector model or the electrical function hole position, etc., will require the wiring harness to be changed synchronously. Generally, the wiring harness design is divided into two aspects: external design and internal design.
The external design change of the automobile wiring harness refers to the technical design change initiated by the client. It mainly involves adding or subtracting functional branches, changing the direction of the wiring harness, changing the functional sheath, changing the installation position of the wiring harness accessories, etc., and mostly focusing on functional design changes.
The internal design change of automobile wiring harness refers to the process of optimizing and changing the product during the process of manufacturing the wiring harness. This process mostly focuses on product optimization and perfect product technology.
Both internal and external design changes have a non-negligible impact on product quality. But in comparison, if the external implementation of the design changes is not in place or the implementation is not thorough, it will affect the assembly progress of the client vehicle, and even more will cause the assembly line to stop and cause quality accidents. So how to achieve batch management when the product is undergoing design changes?
Due to the characteristics of the wiring harness industry, after the first trial assembly of a new product is qualified, the client will issue an order to the wiring harness manufacturer according to market demand. During this period, the client may develop multiple products with different configurations due to changes in market positioning. At this time, product technical changes will be issued. Require component manufacturers, including wire harnesses, to make design changes to their products. This process will require the wire harness manufacturer to make changes to the product at each stage. Including products within the company (pre-invested products, products in process, finished products), products in transit, and client-side products (triple library, RDC library). How to clear the inventory and modify the products in the above three areas will directly affect the final state of the products that reach the client?
Under normal circumstances, the client will consider the actual inventory situation of the supplier involved when issuing design changes, and finally determine the deadline for the new status to reflect. In this process, different manufacturers have different solutions on how to design and change their own products.
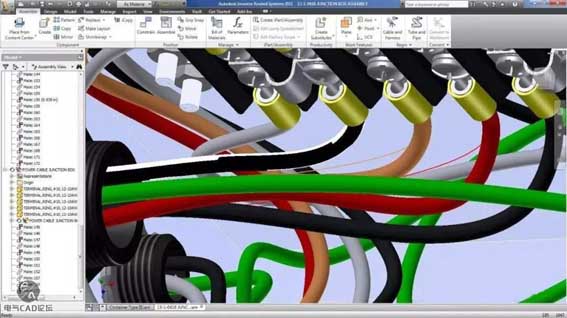
Generally speaking, the marketing department will first track the product transition deadline and report the remaining inventory quantity to the company's internal order logistics department after digestion in the foreign warehouse. The order logistics department counts the final internal and external inventory of the company, including semi-finished products. The technical department prepares and issues design change plans according to the products at different stages, and the manufacturing department implements design changes for all products in accordance with the change plans issued by the technical department. The quality department tracks the implementation of design changes and changes throughout the process. And make a record of the process, and finally summarize the entire implementation process involving changes, and release the results of the implementation.
The entire process described above is a standard process under normal circumstances, but the specific progress and process in the process of specific investigation and inventory must be carried out in accordance with actual customer needs. For example, design changes that affect the functionality of the vehicle must be implemented, and the normal operation of the client production line must be ensured to ensure that the vehicle can be rolled off the line normally without affecting its dynamic testing.
Due to the characteristics of the wiring harness industry, after the first trial assembly of a new product is qualified, the client will issue an order to the wiring harness manufacturer according to market demand. During this period, the client may develop multiple products with different configurations due to changes in market positioning. At this time, product technical changes will be issued. Require component manufacturers, including wire harnesses, to make design changes to their products. This process will require the wire harness manufacturer to make changes to the product at each stage. Including products within the company (pre-invested products, products in process, finished products), products in transit, and client-side products (triple library, RDC library). How to clear the inventory and modify the products in the above three areas will directly affect the final state of the products that reach the client?
Under normal circumstances, the client will consider the actual inventory situation of the supplier involved when issuing design changes, and finally determine the deadline for the new status to reflect. In this process, different manufacturers have different solutions on how to design and change their own products.
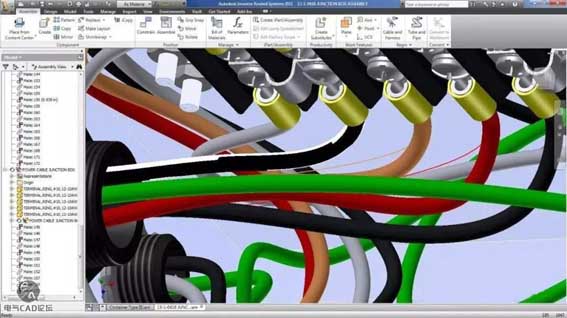
Generally speaking, the marketing department will first track the product transition deadline and report the remaining inventory quantity to the company's internal order logistics department after digestion in the foreign warehouse. The order logistics department counts the final internal and external inventory of the company, including semi-finished products. The technical department prepares and issues design change plans according to the products at different stages, and the manufacturing department implements design changes for all products in accordance with the change plans issued by the technical department. The quality department tracks the implementation of design changes and changes throughout the process. And make a record of the process, and finally summarize the entire implementation process involving changes, and release the results of the implementation.
The entire process described above is a standard process under normal circumstances, but the specific progress and process in the process of specific investigation and inventory must be carried out in accordance with actual customer needs. For example, design changes that affect the functionality of the vehicle must be implemented, and the normal operation of the client production line must be ensured to ensure that the vehicle can be rolled off the line normally without affecting its dynamic testing.
Through this example, just to express the importance of design change implementation. Of course, after a component is mass-produced, it may involve multiple design changes and optimization processes. During the period, the design change optimization and its matching synchronization state deeply affect its current assembly state, and the adaptability of the state also has a significant impact on the overall quality of the vehicle.
Of course, the content of the design change is different, and the result is also different. Therefore, it is very necessary to implement batch management for the state of wire harness design changes. He not only has an important influence on the confirmation of product status, but also has an equally important influence on the control of the number of product batches within the company. So, how to ensure that different states correspond to the corresponding design change batch management in actual production?
How to achieve simultaneous control of internal design changes and external design changes?
There are two management methods that I have come across. One is to replace and seal the drawings. The company's internal data management room conducts centralized management of the drawing status to ensure that the latest status of the customer's order plan is used on site. According to the status number, the process will be inspected and packaged sequentially, and the batch status of the product will be marked on the product and the outer box; Another method is to take the form of design variable codes for internal and external change management, and their respective codes are changed according to certain regular data to reflect the product status under different design variable batches. Compared with the first form, there are similarities and similarities, but the manifestation of design changes is different.
Through the summary of the above process, I will share my experience with you here, but even if there is a complete standard process for this process, there is still no lack of unity and cooperation between various departments. Only with the double cooperation of standards and inter-departmental communication, the work will be carried out more smoothly.
How to achieve simultaneous control of internal design changes and external design changes?
There are two management methods that I have come across. One is to replace and seal the drawings. The company's internal data management room conducts centralized management of the drawing status to ensure that the latest status of the customer's order plan is used on site. According to the status number, the process will be inspected and packaged sequentially, and the batch status of the product will be marked on the product and the outer box; Another method is to take the form of design variable codes for internal and external change management, and their respective codes are changed according to certain regular data to reflect the product status under different design variable batches. Compared with the first form, there are similarities and similarities, but the manifestation of design changes is different.
Through the summary of the above process, I will share my experience with you here, but even if there is a complete standard process for this process, there is still no lack of unity and cooperation between various departments. Only with the double cooperation of standards and inter-departmental communication, the work will be carried out more smoothly.