Customized automotive wiring harness supplier (pune maharashtra wiring, engine wiring kit)
- PRODUCT DETAIL
The automobile wiring harness is the main body of the automobile circuit, and there is no automobile circuit without the wiring harness. The wiring harness refers to the contact terminal (connector) made of copper material, after crimping the wire and cable, and then plasticizing an insulator or adding a metal shell on the outside. Bundled with wire harnesses to form components that connect circuits. The wire harness industry chain includes wire and cable, connectors, processing equipment, wire harness manufacturing and downstream application industries. Wire harnesses are widely used and can be used in automobiles, household appliances, computers and communication equipment, various electronic instruments and meters. The car wiring harness connects the entire car body, and the general shape is H-shaped.
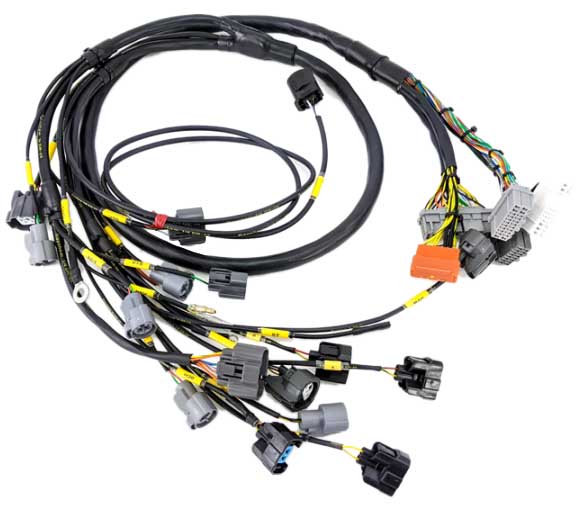
Basic introduction to automotive wiring harness
The wires of automobile wiring harnesses are also called low-voltage wires, which are different from ordinary household wires. Ordinary household wires are copper single-core wires with certain hardness. Automotive wires are copper multi-core cords, some cords are as thin as hair, and several or even dozens of flexible copper wires are wrapped in a plastic insulating tube (polyvinyl chloride), which is soft and not easy to break.
Due to the particularity of the automotive industry, the manufacturing process of automotive wiring harnesses is also more special than other ordinary wiring harnesses.
The systems for manufacturing automotive wiring harnesses are roughly divided into two categories:
1. Divided by European and American countries, including China:
Use TS16949 system to control the quality of the manufacturing process.
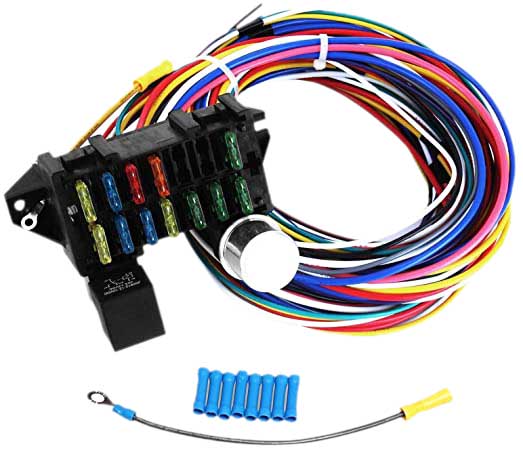
Arrangement of automobile wiring harness
Before arranging the wiring harness, draw the wiring harness diagram in advance. The wiring harness diagram is different from the circuit schematic diagram.
A schematic circuit diagram is an image that expresses the relationship between various electrical parts. It does not reflect how the electrical components are connected to each other, and is not affected by the size and shape of each electrical component and the distance between them. The wiring harness diagram must take into account the size and shape of each electrical component and the distance between them, and also reflect how the electrical components are connected to each other.
After the technicians of the wiring harness factory make the wiring harness wiring board according to the wiring harness diagram, the workers cut and arrange the wires according to the wiring board regulations. The main wiring harness of the whole vehicle is generally divided into the engine (ignition, electronic injection, power generation, starting), instrumentation, lighting, air conditioning, auxiliary electrical appliances, etc. There are main wiring harness and branch wiring harness. A whole vehicle main harness has multiple branch harnesses, just like tree poles and branches. The main wiring harness of the whole vehicle often takes the instrument panel as the core part, extending front and rear. Due to the length relationship or the convenience of assembly, some automobile wiring harnesses are divided into front wiring harness (including instrumentation, engine, headlight assembly, air conditioner, battery), rear wiring harness (tail light assembly, license plate light, luggage compartment light), roof Wiring harness (car doors, ceiling lights, audio speakers), etc. Each end of the wire harness will be marked with a logo number and letter to indicate the connection object of the wire. The operator can see that the logo can be correctly connected to the corresponding wire and electrical device, which is particularly useful when repairing or replacing the wire harness. At the same time, the color of the wire is divided into a single color line and a two-color line, and the use of the color is also specified, which is generally a standard set by the car factory. my country's industry standards only stipulate the main color. For example, it is stipulated that single black is used for grounding wires, and red and single color is used for power wires.
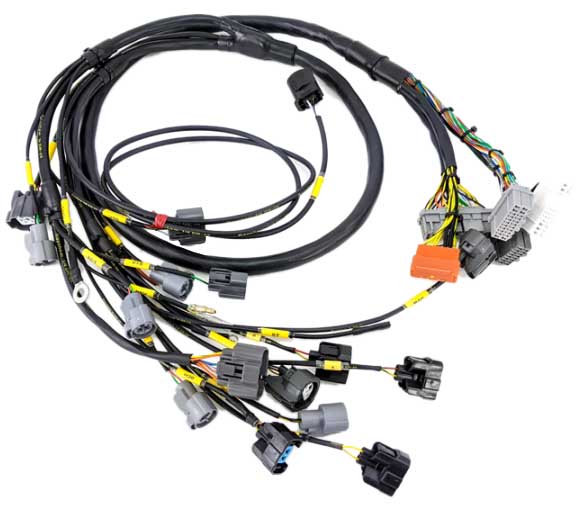
Basic introduction to automotive wiring harness
The wires of automobile wiring harnesses are also called low-voltage wires, which are different from ordinary household wires. Ordinary household wires are copper single-core wires with certain hardness. Automotive wires are copper multi-core cords, some cords are as thin as hair, and several or even dozens of flexible copper wires are wrapped in a plastic insulating tube (polyvinyl chloride), which is soft and not easy to break.
Due to the particularity of the automotive industry, the manufacturing process of automotive wiring harnesses is also more special than other ordinary wiring harnesses.
The systems for manufacturing automotive wiring harnesses are roughly divided into two categories:
1. Divided by European and American countries, including China:
Use TS16949 system to control the quality of the manufacturing process.
2. Mainly Japanese automobile wiring harness:
For example, Toyota and Honda have their own systems to control the manufacturing process.
With the increase of automobile functions and the widespread application of electronic control technology, there are more and more electrical parts and more and more wires, and the wire harness becomes thicker and heavier. Therefore, advanced cars have introduced CAN bus configuration and adopted multiple transmission systems. Compared with the traditional wiring harness, the multiple transmission device greatly reduces the number of wires and connectors, making wiring easier.
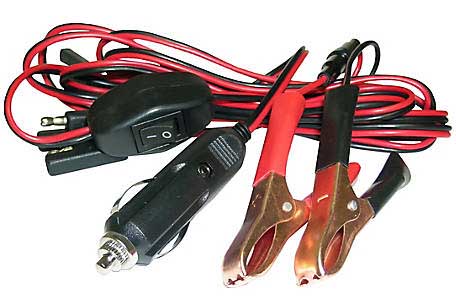
For example, Toyota and Honda have their own systems to control the manufacturing process.
With the increase of automobile functions and the widespread application of electronic control technology, there are more and more electrical parts and more and more wires, and the wire harness becomes thicker and heavier. Therefore, advanced cars have introduced CAN bus configuration and adopted multiple transmission systems. Compared with the traditional wiring harness, the multiple transmission device greatly reduces the number of wires and connectors, making wiring easier.
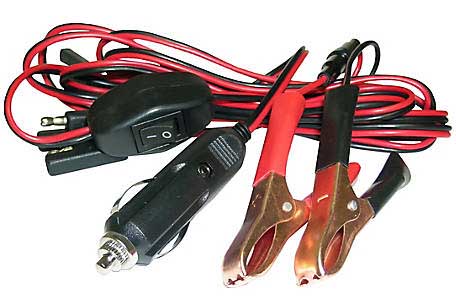
Commonly used car wiring harness wires
Common specifications for wires in automotive wiring harnesses include wires with a nominal cross-sectional area of 0.5, 0.75, 1.0, 1.5, 2.0, 2.5, 4.0, and 6.0 square millimeters. (The nominal cross-sectional area commonly used in Japanese cars is 0.5, 0.85, 1.25, 2.0, 2.5, 4.0, 6.0, etc. square millimeters). Each of them has an allowable load current value and is equipped with wires for different power consumption equipment.
Take the wiring harness of the whole vehicle as an example, the 0.5 specification wire is suitable for instrument lights, indicator lights, door lights, ceiling lights, etc.;
The 0.75 specification line is suitable for license plate lights, front and rear small lights, brake lights, etc.;
1.0 specification line is suitable for turn signal, fog lamp, etc.;
1.5 specification line is suitable for headlights, speakers, etc.;
Main power lines such as generator armature lines, grounding lines, etc. require 2.5 to 4 square millimeter wires. This only refers to the general car. The key is to look at the maximum current value of the load. For example, the ground wire of the battery and the positive power wire are dedicated car wires for separate use. Their wire diameter is relatively large, at least more than ten square millimeters, these "big and thick" wires will not be woven into the main wiring harness.
Take the wiring harness of the whole vehicle as an example, the 0.5 specification wire is suitable for instrument lights, indicator lights, door lights, ceiling lights, etc.;
The 0.75 specification line is suitable for license plate lights, front and rear small lights, brake lights, etc.;
1.0 specification line is suitable for turn signal, fog lamp, etc.;
1.5 specification line is suitable for headlights, speakers, etc.;
Main power lines such as generator armature lines, grounding lines, etc. require 2.5 to 4 square millimeter wires. This only refers to the general car. The key is to look at the maximum current value of the load. For example, the ground wire of the battery and the positive power wire are dedicated car wires for separate use. Their wire diameter is relatively large, at least more than ten square millimeters, these "big and thick" wires will not be woven into the main wiring harness.
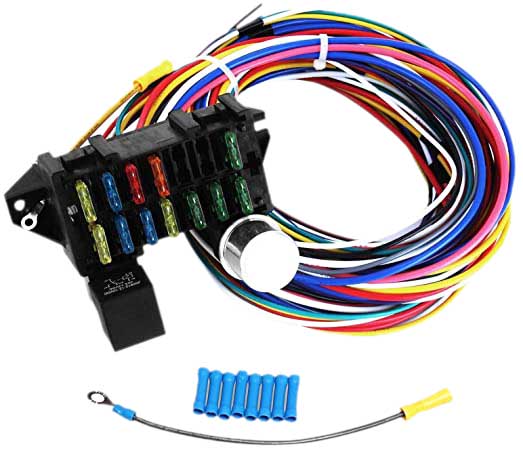
Arrangement of automobile wiring harness
Before arranging the wiring harness, draw the wiring harness diagram in advance. The wiring harness diagram is different from the circuit schematic diagram.
A schematic circuit diagram is an image that expresses the relationship between various electrical parts. It does not reflect how the electrical components are connected to each other, and is not affected by the size and shape of each electrical component and the distance between them. The wiring harness diagram must take into account the size and shape of each electrical component and the distance between them, and also reflect how the electrical components are connected to each other.