What is Cross-Linked Polyethylene Cable (XLPE)?
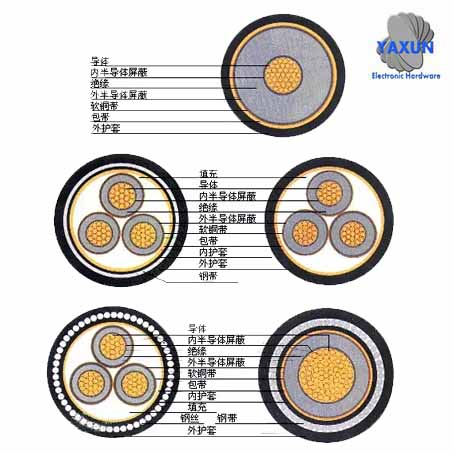
XLPE cable is a kind of cross-linked polyethylene cable, which occupies an extremely important position in the power supply grid. XLPE cable is a kind of cable suitable for power distribution network and other fields, and has the advantages that PVC insulated cables can't compare. It has simple structure, light weight, good heat resistance, strong load capacity, non-melting, chemical corrosion resistance, and high mechanical strength.
Enough attention should be paid to the safety and reliability of XLPE power cable line operation. Necessary and appropriate measures must be taken to prevent accidents and monitor the operating conditions of power cable lines. The test plan of XLPE cable mainly includes withstand voltage test, routine state assessment and partial discharge test. The main part that can be used for cable testing in field operation is partial discharge testing.
Introduction to XLPE cable
Cross-linked cables usually refer to the use of cross-linked materials in the insulation layer of the cable. The most commonly used material is cross-linked polyethylene (XLPE).The cross-linked polyethylene insulated cable uses chemical or physical methods to transform the polyethylene molecule of the cable insulation from a linear molecular structure to a main network molecular structure. That is, thermoplastic polyethylene is transformed into thermosetting cross-linked polyethylene. Thereby greatly improving its heat resistance and mechanical properties, reducing its shrinkage, making it no longer melted after being heated, and maintaining excellent electrical properties.
The long-term allowable working temperature of XLPE cables is increased from 70°C to 90°C (or higher). The allowable temperature is increased from 140°C to 250°C (or higher) during short-circuit, which greatly improves the actual use performance while maintaining its original excellent electrical performance.
The safe operation of the XLPE cable is very important to the stability of the entire power system. Once a failure occurs, it will cause a major power outage in the area under its jurisdiction. Based on the analysis of materials such as the records of power cable repairs in major cities throughout the year, photos of the accident site, and sealing samples of faulty cables. The causes of power cable operation failures can be divided into four types: External force damage, cable accessory manufacturing quality, cable laying and installation quality, and cable body manufacturing quality accounted for 58%, 27%, 12%, and 3% respectively. Excluding faults caused by external force damage, cable accessory faults account for more than 50% of cable operating faults. However, more than 97% of the cable accessory failures are insulation failures caused by the surface discharge of the solid composite medium. It can be seen that the operation of XLPE power cable lines, especially the safety and reliability of the operation of cable accessories, should be given sufficient attention. Necessary and appropriate measures must be taken to prevent accidents and monitor the operating conditions of power cable lines.
XLPE cable performance
Cross-linked polyethylene insulated cables use peroxide cross-linking methods to change polyethylene molecules from linear molecular structures to three-dimensional network structures, and from thermoplastic materials to thermosetting materials. The working temperature is increased from 70°C to 90°C, which significantly improves the current-carrying capacity of the cable. XLPE insulated cables have the following advantages:1. Heat resistance: The XLPE with a net-like three-dimensional structure has excellent heat resistance. It will not decompose and carbonize below 300℃, the long-term working temperature can reach 90℃, and the thermal life can reach 40 years.
2. Insulation performance: XLPE maintains the original good insulation properties of PE, and the insulation resistance is further increased. The dielectric loss tangent value is very small, and it is not greatly affected by temperature.
3. Mechanical characteristics: Due to the establishment of new chemical bonds between macromolecules, the hardness, stiffness, wear resistance and impact resistance of XLPE have been improved, thus making up for the shortcomings of PE being vulnerable to environmental stress and cracking.
4. Chemical resistance: XLPE has strong acid and alkali resistance and oil resistance. Its combustion products are mainly water and carbon dioxide, which are less harmful to the environment and meet the requirements of modern fire safety.
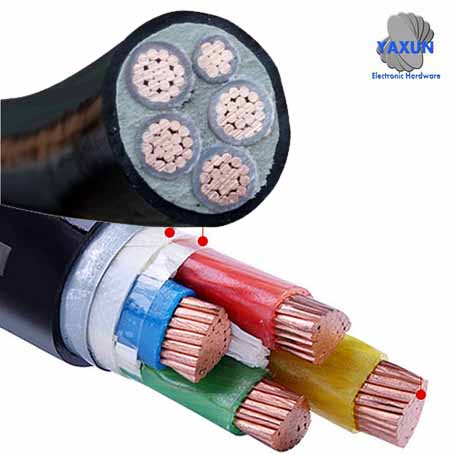
Application of XLPE cable
Cross-linked polyethylene insulated cables are suitable for power distribution networks, industrial installations or other fields that require large-capacity electricity. It is used for fixed laying on power transmission and distribution lines with AC 50Hz and rated voltage 6kV~35kV. The main function is to transmit electric energy.Key technical issues of XLPE cables
Although cross-linked polyethylene (XLPE) has many outstanding advantages as an insulating material, and some excellent products have been developed after years of hard work, there are still some important problems that need to be solved. From the perspective of the HVDC power transmission cable market, traditional HVDC power transmission cables such as impregnated paper-insulated cables or oil-filled cables are still mainstream products, and improvements are still being made on this basis. It can be seen from the products produced by the two largest cable companies, Presman in Italy and Nexans in France. In terms of the products of 500kV and above HVDC transmission cables, oil-filled-paper insulated cables are still the absolute mainstream products. In contrast, 500kV HVDC XLPE insulated cables are only in the test certification stage in Japan without commercial certification. Although ABB’s light-duty high-voltage DC transmission cables have passed commercial certification for 80kV, 150kV and 320kV, they are only applied to engineering projects with two voltage levels of 80kV and 150kV. From this, it can be seen that increasing the voltage level and capacity is the development direction of high-voltage DC XLPE insulated cable products, which also puts forward corresponding technical requirements.From a technical point of view, the space charge generated and accumulated during the HVDC transmission process of XLPE insulated cables is the most important problem that polymer insulation materials need to face. It has always limited the application of polymer insulation materials in HVDC cables. Therefore, both the mechanism of space charge accumulation and the suppression of space charge accumulation are the focus of research: Including the corresponding polymer insulation material in the cable semiconductor- Interface properties of insulators and semiconductor materials- Research on insulator materials, research on the properties of insulator interfaces, the effect of temperature gradient on space charge, the process of space charge accumulation, etc.
Of course, it also includes some other issues: The mechanism of insulation material aging, the long-term stability of new materials, and the influence of partial discharge. It is not clear whether the upper limit of the operating voltage should be determined by the measurement of space charge or by the threshold voltage of electrical aging.
XLPE cable breakdown identification method
Identify the false breakdown method of XLPE cable:In the process of using the series resonance test system to perform partial discharge and high voltage tests of the finished medium voltage cable products, sometimes false breakdowns suddenly appear during the test due to various reasons: How to correctly identify the true breakdown of the cable itself or the false breakdown of the cable due to other reasons is of great significance for improving the efficiency of the cable factory test.
The factory partial discharge and high voltage tests of medium voltage XLPE power cables are carried out one by one in the shielded room. At this time, you can consider replacing the insulated core for retesting. If the voltage test passes normally after the core is replaced, it should be determined that the cable has really broken down. Or, re-boost, if the breakdown voltage shows a gradual decrease, it can also be determined that the cable has a true breakdown. If the breakdown voltage of the cable is at the same value every time, it should be considered whether the cable end has a breakdown. At this time, the door interlock switch of the door of the partial discharge shielding room can be manually closed, and the door of the shielding room can be opened to increase the voltage, observe the breakdown phenomenon, and quickly determine the end breakdown position. If after investigation, there is no breakdown at the end of the cable, replace multiple insulated cores and cables, and even retest the cables that have been qualified by Zengjin or no-load retests. The breakdown voltage always maintains the same value. It should be possible to confirm that a false breakdown occurred in the cable, and the equipment should be inspected; the test should be performed after troubleshooting. However, for some long-length single-core medium-voltage cross-linked cables that have been inspected, it should be checked whether they have exceeded the allowable load of the test equipment. In this case, detuning and tripping will also occur during the test process, and it is not necessary to rashly determine that the cable has broken down.
There is a special case that needs to be explained here. Sometimes a short circuit occurs inside the cable insulation, and the series resonance test system may not be able to resonate to boost the voltage. This is also a special cable breakdown phenomenon. In case of this phenomenon, it can be confirmed after the test by replacing the well-insulated wire core.
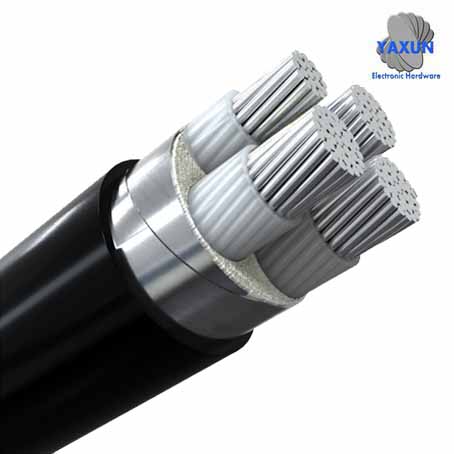
XLPE cable manufacturing process
The process methods for producing XLPE cables are divided into three categories:The first category "peroxide chemical crosslinking" includes saturated vapor crosslinking, inert gas crosslinking, molten salt crosslinking, and silicone oil crosslinking. The second most common method is dry chemical cross-linking;
Type 2, silane chemical crosslinking;
Type 3, radiation cross-linking.
Inert gas
It adopts polyethylene insulating material added with peroxy compound cross-linking agent, which is completed by three-layer co-extrusion: the extrusion of the shielding layer of the conductor-the insulating layer-the insulating shielding layer. Continuously and uniformly complete the cross-linking process through a sealed cross-linking tube filled with high temperature and high pressure nitrogen. The heat transfer medium is nitrogen (inert gas), the cross-linked polyethylene has excellent electrical properties, and the production range can reach 500KV.
Silane Chemistry
Adopt polyethylene insulation material added with silane crosslinking agent, and complete it by 1+2 extrusion method: conductor shielding layer-insulating layer-insulating shielding layer. Immerse the cooled insulated wire core in 85-95℃ hot water for hydrolysis and cross-linking, because wet cross-linking will affect the water content in the insulating layer. Generally, the highest voltage level is only 10KV.
Latest technology
Application method of chemical crosslinking and radiation crosslinking functional mother particles
Using polyethylene cable with cross-linking function mother particles, a small amount of this function mother particles can be added to the material particles of ordinary polyethylene cables, and the extruded cable can become a cross-linked cable.
There are three types of cable cross-linking functional mother particles: Chemical cross-linking function, electron beam irradiation cross-linking function, ultraviolet light irradiation cross-linking function.
1. The mother particle with cross-linking function for chemically cross-linked cables, model: DH-125Y,
The appearance of DH-125Y chemically crosslinked functional mother particles is colorless LLDPE plastic particles. Wire and cable factories only need to purchase common LLDPE polyethylene plastic particles on the market, such as LLDPE 7042 and so on. Add 1 kilogram of DH-125Y functional mother particles to 25 kilograms of LLDPE7042 plastic particles, turn them evenly by hand, and directly put them into the extruder for cables and wires. Extruding the cable, that is, a chemically cross-linked cable is made. The functional mother particles can produce cross-linked wires and cables of 35KV and below.
2. Cross-linking functional mother particles for electron beam irradiation cross-linked cables, model: DH-125DF
The appearance of the DH-125DF electron beam radiation crosslinking function mother particles is colorless LLDPE plastic particles. 1 kg of DH-125DF functional mother particles are added to 7042 plastic particles. After turning it evenly by hand, put it directly into the extruder to extrude the cable. Then irradiated by electron beams to make a cross-linked cable. This functional mother particle can produce cross-linked cables with a long-term working temperature of 125℃ in the environment.
3. Ultraviolet light irradiation cross-linked cable uses cross-linking functional mother particles, model: DH-125ZF,
The appearance of DH-125ZF UV-irradiated cross-linking functional mother particles is colorless LLDPE plastic particles. 1 kg of DH-125ZF functional mother particles are added to 7042 plastic particles. After turning it evenly by hand, it is directly put into the extruder of the cable and wire, and the cable is extruded, and the cross-linked cable is made by ultraviolet light irradiation. The mother particles of this function can produce cross-linked wires and cables with a long-term working environment temperature of 125°C.
advantage:
1. Save money:
Reduce costs. It can be used directly by the cable manufacturer, which is 1500~3000 yuan/ton cheaper than the chemical and radiation cross-linked polyethylene cable special particles purchased in the market.
2. Time saving;
The time period of about one week for inquiring, ordering, production, and transportation is needed for the cable manufacturer to purchase chemical and irradiated cross-linked polyethylene cable special material particles. When using DH-125 functional mother particles, after deciding on the production plan, the cable can be directly produced after 5 minutes of preparation.
3. Versatility,
The cable manufacturer can adjust the variety and hardness of its own: DH-125 functional mother particles can not only be added to ordinary polyethylene PE particles, but also can be added to ordinary cable material particles that do not have cross-linking properties. Turn ordinary plastic cable particles that do not have cross-linking properties into cross-linked plastic particles.
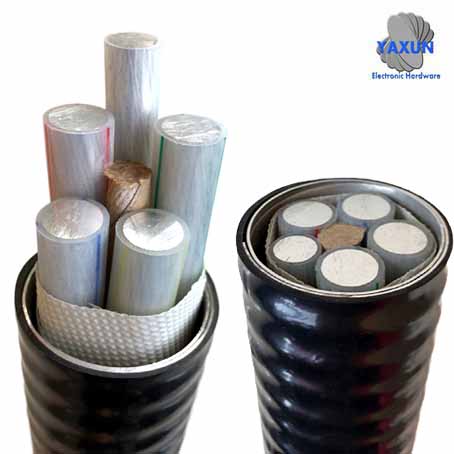
Radiation crosslinking
The modified polyethylene insulating material is used through 1+2 extrusion method: the extrusion of the foreign body shielding layer-the insulating layer-the insulating shielding layer. Pass the cooled insulated wire core uniformly through the radiation scanning window of the high-energy electron accelerator to complete the cross-linking process. No cross-linking agent is added to the radiation cross-linked cable material. During cross-linking, the high-energy electron beam generated by the high-energy electron accelerator effectively penetrates the insulating layer, and the cross-linking reaction is generated through energy conversion. Because electrons have high energy and pass through the insulating layer uniformly, the cross-linked bonds formed have high binding energy and good stability. The physical performance shown is that the heat resistance is better than that of chemically cross-linked cables. However, due to the limitation of the energy level of the accelerator (generally no more than 3.0Mev, the effective penetration thickness of the electron beam is less than 10mm). Considering geometric factors, the voltage level of the production cable can only reach 10KV, and the advantage is below 6KV.There are many types of cross-linked cable insulation, which are mainly divided into two categories from the cross-linking mechanism, namely, physical cross-linking and chemical cross-linking.
1. Chemical crosslinking:
There are two methods of high temperature crosslinking and low temperature crosslinking.
(1) High temperature crosslinking is also called peroxide crosslinking. Generally, organic peroxides are used as crosslinking agents, which decompose to generate active free radicals under the action of heat. These free radicals generate active sites on the polymer carbon chain and generate C-C cross-linking bonds to form a three-dimensional network structure. High-temperature cross-linking includes steam cross-linking and dry cross-linking. Most of the cross-linked cables used steam cross-linking process in the 1960s. As the steam cross-linking increases the moisture content in the insulation, the insulation quality is not good, and it has been completely eliminated; Since the 1970s, the dry cross-linking process has been widely used in foreign countries, using high-pressure vulcanization pipelines and rapid heating methods for cross-linking.
(2) Low temperature crosslinking is also called warm water crosslinking or silane crosslinking. The cable is cross-linked in warm water at 70-90 ℃, and the cross-linking agent in the insulation-silane, after absorbing water, the linear structure reacts to form a network-like cross-linked structure.
2. Physical cross-linking: also known as radiation cross-linking.
It is divided into two methods: γ-ray crosslinking and electron beam crosslinking.
(1) γ-ray cross-linking is only used in the cross-linking of heat-shrinkable materials due to its low dose rate and cannot penetrate the core wire of the cable during irradiation. Generally, γ-ray cross-linking is not used in the production of wires and cables.
(2) Electron beam crosslinking: Use an electron accelerator to cooperate with an irradiation device, and use a high-energy electron beam (generally between 1.0-3.0 MeV) to irradiate the insulation layer of the cable. Initiate polymer materials to generate free radicals, form C-C cross-links, and generate a three-dimensional network structure.
Performance comparison
Performance comparison of commonly used insulated cables:In cable production, the most commonly used insulating plastics are polyethylene and polyvinyl chloride. Among them, polyethylene materials have better electrical properties and better cross-linking properties, so a variety of industrial cross-linking production processes, chemical cross-linking and radiation cross-linking have been developed. In the process of production and laying, the insulation layer of commonly used cross-linked cables has higher hardness and strength, which is more difficult to peel off than PVC insulation. Since the spoke cross-linked cable has the best cross-linking performance and the highest degree of cross-linking, relatively speaking, the peel strength is also the highest. If the peeling of the cross-linked cable insulation layer is relatively easy (similar to polyvinyl chloride), it must be insufficient or no cross-linking. Under normal circumstances, the cross-linked cables produced by the warm water cross-linking process often have insufficient cross-linking degree, because the original cross-linking degree of this kind of products is relatively low. Moreover, the cross-linking process is non-continuous and cannot be automatically controlled. It is greatly affected by human factors and is prone to under-cross-linking.
Irradiation cross-linked cable characteristics:
The aging life of cable insulation material mainly depends on its thermal aging life. It is determined by the speed of chemical reactions such as thermal oxygen oxidation, thermal cracking, thermal oxidative cracking, and polycondensation that occur in the insulating material under hot working. Therefore, the thermal aging life of the insulating material directly affects the service life of the cable. According to the chemical reaction kinetics derivation and the artificial accelerated thermal aging test (20-30 years), the long-term allowable working temperature of the irradiated cross-linked cable is:Power cable YJV 0.6/1KV
The rated working temperature is 105 degrees, and its thermal aging life is more than 60 years.
The rated working temperature is 90 degrees, and its thermal aging life is more than 100 years.
Overhead insulated cable
When overhead insulated cables are laid in the open air, the environmental resistance and radiation resistance of the insulating materials are more important. Irradiation cross-linked insulating materials have to undergo irradiation processing, and they themselves have good radiation resistance. The radiation dose applied in the cross-linking production process leaves a large safety margin from the destruction dose. The radiation damage dose of polyethylene is 1000KGY, and the processing dose is about 200KGY. Coupled with the improvement of the special formula, it is still cross-linked by radiation in a relatively wide range, so its performance will be improved when exposed to radiation during a longer period of use.