Electrical Connectors are Classified According to Purpose, Appearance and Structure
- PRODUCT DETAIL
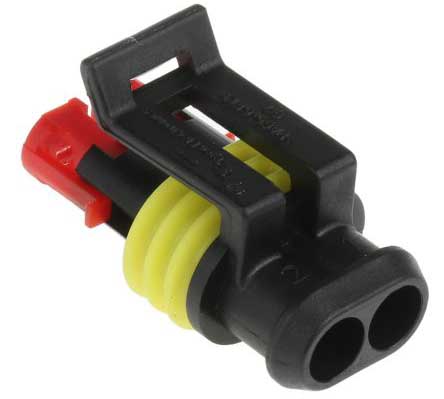
In addition to meeting general electrical performance requirements for electrical connectors, a particularly important requirement is that electrical connectors must achieve good contact, reliable work, and convenient maintenance. The reliability of its work directly affects the normal operation of the equipment circuit, and involves the safety of the entire host. For this reason, the host circuit has very strict requirements on the quality and reliability of the electrical connector. It is also because of the high quality and high reliability of the electrical connector that it is also widely used in military systems such as aviation, aerospace, and national defense. Commonly used classification methods for electrical connectors include shape, structure, and purpose.
Introduction to electrical connectors
In various military aircraft and weapon equipment, the amount of electrical connectors is relatively large, especially the amount of electrical connectors used on aircraft. Generally speaking, an aircraft's electrical connector can be used in hundreds to thousands of pieces, involving tens of thousands of circuits.
Electrical connector classification
Classified by shape
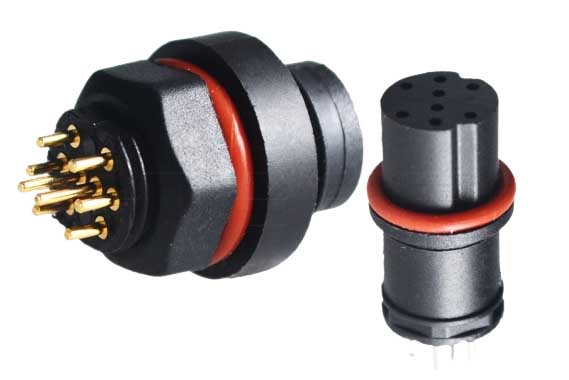
Circular electrical connectors, rectangular electrical connectors.
Circular electrical connectors have the largest amount of use in military equipment (aviation and aerospace) due to their structural characteristics. Due to its simple structure, rectangular electrical connectors are more commonly used on printed circuit boards of electronic equipment.
Classified by structure
According to the connection method: Threaded connection, bayonet (quick) connection, card lock connection, push-pull connection, in-line connection, etc.;
According to the contact body termination form: crimping, welding, winding; screw (cap) fixing;
Classified by environmental protection: Environmental resistant electrical connectors and ordinary electrical connectors.
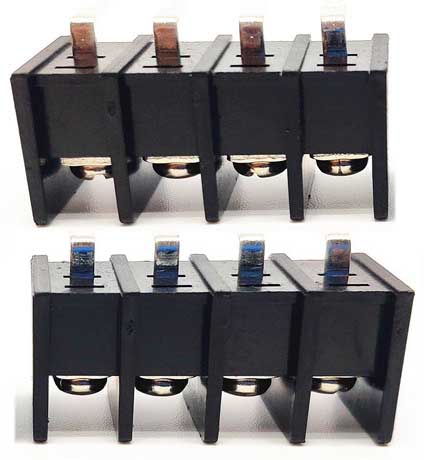
Classified by purpose
RF electrical connector
Sealed electrical connector (glass sealing welding)
High temperature electrical connector
Automatic disconnection and separation electrical connector
Filtering electrical connector
Composite electrical connector
Airport power connector
Electrical connectors for printed circuit boards, etc.
Structure of electric connector
The electrical connector is composed of a fixed-end electrical connector, that is, a female contact (socket), and a free-end electrical connector, that is, a male contact (a plug for short). The socket is fixed on the electrical component through its square plate (circle) (individually, welding is also used). The plug is generally connected to the cable, and the plug and socket are connected through the connecting nut.
The electrical connector is composed of three basic units: a shell, an insulator, and a contact.
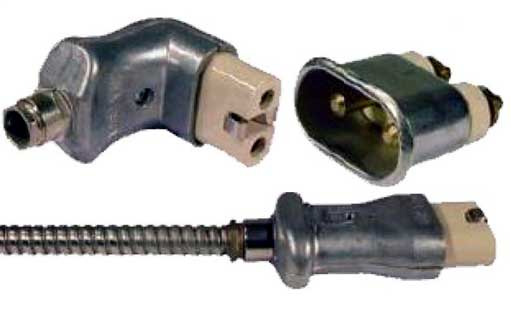
The electrical connector shell refers to the shell of the plug socket, the connection nut, and the tail attachment. The function of the shell is to protect the internal parts of the electrical connector such as the insulator and the contact body (the general name of the pin socket) from being damaged. The upper positioning key groove ensures the positioning of the plug and the socket. The connecting nut is used to connect and disconnect the plug socket. The tail attachment is used to protect the wire and the contact body from damage and to fix the cable. The shell also has a certain electromagnetic shielding effect.
The shell is generally made of aluminum alloy processing (machined, cold extrusion, die-casting). Steel shells are mostly used for glass sealing and welding and high-temperature electrical connectors.
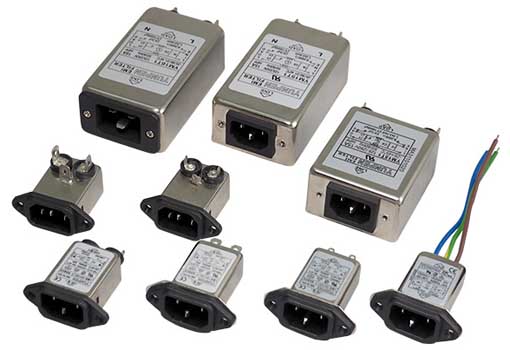
Insulator of electrical connector
The insulator has an insulator mounted pins, an insulator mounted jack. Interface seal member, wire sealing body and other components. It is used to keep the pins and sockets in the set positions, and electrically insulate each contact body and between each contact body and the shell. The sealing measures are obtained by the insulator and the interface sealing body sealing body to improve the environmental resistance of the electrical connector.
In order to adapt to the high temperature, low temperature and flame retardant of the product, the geometric dimensions of the parts are stable and reliable. Insulators are mostly molded from thermosetting plastics. The interface sealing body and the wire sealing body are molded by silicon rubber.
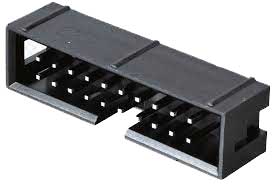
Contact body of electric connector
The contact body includes a male contact piece and a female contact piece, sometimes also called a pin jack. The connection method is divided into welding type, crimping type, pressing-in type and winding type, etc. to realize circuit connection.
The pin jack is a key element of the electrical connector, which directly affects the reliability of the electrical connector. Most of the pins and sockets are machine-added with elastic copper alloy materials with good electrical conductivity, and the surface is silver-plated and gold-plated to achieve low contact resistance and corrosion resistance. The jacks generally include split slot jacks, wire spring jacks, crown spring jacks, and punched jacks.
The structural features are: Resistant to atmospheric environment, bayonet type (fast) connection, multi-key position (anti-error insertion). The contact body is crimped and connected with the wire (single wire is taken and sent for easy troubleshooting). The shell and shielding ring ensure 360° electromagnetic interference shielding ability.