Technical Difficulties in Injection Molding Production of Connectors and Terminals
- PRODUCT DETAIL
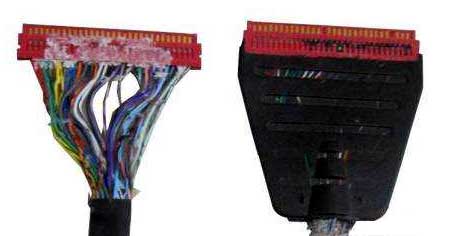
I. The main reasons for the concave and uneven injection molded terminals:
1. Design the large gate to solidify in advance and cannot cover the area and shrink; The material should be selected appropriately to reduce the thickness of the meat, the size of the gate should be increased to facilitate the filling of the plastic, and the gate should be designed in the area with a larger thickness.
2. Improper setting of molding conditions (holding pressure measurement); Increase the holding pressure and time (not too much).
3. Improper design of the terminal plastic shell product, resulting in serious depression and unevenness;
The thickness of the meat must be average, and the thickness of the reinforcing force must be smaller than the wall thickness.
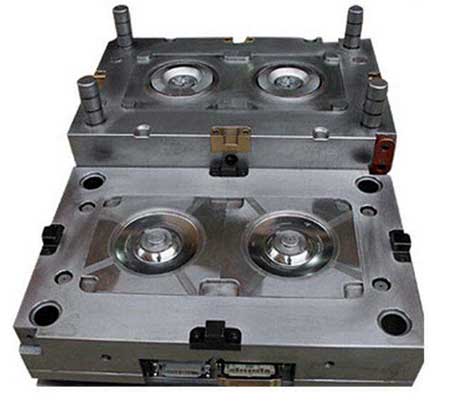
II. Reasons for the poor luster of the injection molded terminal shell:
1. The injection molding connector mold is damaged or poorly ground; it should be mirror-finished with chrome plating or titanium sandpaper polished.
2. The material temperature or mold temperature of the injection connector is too low; Appropriate material temperature and mold temperature should be selected to improve gloss.
III. Reasons for the scorching of the terminal injection case:
1. Poor exhaust, excessive gas content in the plastic itself;
The injection rate should be reduced to strive for the gas discharge time, and the mold core should be divided to increase the exhaust slot. The two-stage mold clamping is first low pressure exhaust, and then high pressure clamping.
IV. The reason for the color mixing of the terminal injection shell:
1. The friction belt electrostatically absorbs dust when the product is injection molded; The storage basket should be equipped with an anti-static device.
2. The processing oil has not been cleaned up, and the machine environment is polluted; Clean out mold oil stains, adhere to clean environment and machine cleaning.
3. When plastic is dried and crushed, it is mixed with auxiliary materials; Note that the machine and the surroundings should use the same color plastic as much as possible.
Ⅴ.Reasons for the deformation of the injection mold core:
1. The corepine is too long and lacks strength; The product should be designed to prevent the core aspect ratio from being greater than 5.
2. The measuring holding pressure is too large; The conditions should be adjusted according to the product pop-up situation.
3. Bending due to injection molding line; The glue line should be moved to a strong area and the cold slug well should be enlarged.
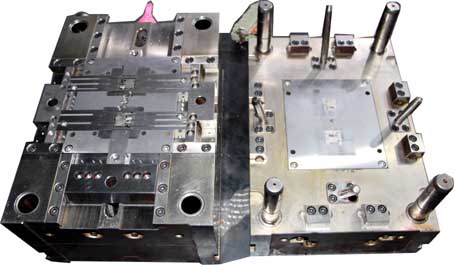
Ⅵ. The reason for the injection molding glue line:
1. Injection molding glue line formed by multi-point injection or unpreventable condition; Increase thickness, temperature or pressure in the glue line area. Move the gate to move the glue line and unimportant areas, and install an overflow well to reduce the phenomenon of injection molding.
Ⅶ, the reason of uneven demolding:
1. Improper product/mold design. When the front end is too large, it is not easy to eject; Add plastic wall thickness to reduce injection pressure, gate and thimble.
2. The ejection system is not balanced, causing the top to penetrate and stick to the mold; Should consider the overall configuration, the material depth area needs to be equipped with thimble on both sides.
3. Improper design of parting line sticks to the master mold and cannot be demolded; Most of the plastic products should be designed on the male mold.
4. Mold core damage or improper assembly, forming hairs and affecting demolding; The mold should be checked and corrected.
5. The dead angle formed by the mold makes it difficult to demold; Grinding and polishing, setting of thimble, design to prevent in the demolding direction.
6. The ejector is not smooth and the thimble is broken; The thimble assembly should not be sloppy "no haste, be patient".
Ⅷ、Reasons for the short shot phenomenon of the connector plastic shell:
1. The uneven wall thickness of the product results in abnormal activity in the thin area, and short shots in severe cases; Try to average the wall thickness when designing.
2. Unbalanced activity of each acupuncture point in the multi-mode acupuncture; Balance the runner design and use mold flow analysis to calculate its size.
3. The specifications of the injection line do not match; Measure the machine based on the product size.
4. Lack of plastic mobility; Adjust the temperature shot pressure to improve (refueling).
5. Short shots due to poor exhaust; Increase the exhaust slot and reduce the rate of fire.
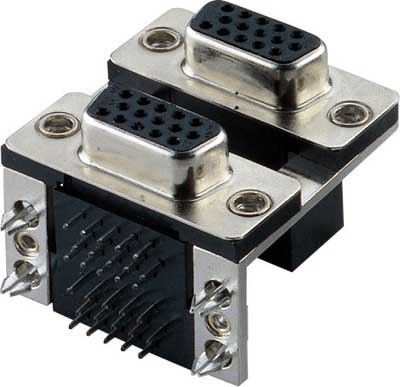
Ⅸ、Reasons for warping and deformation of the connector plastic shell:
1. The uneven wall thickness of the product results in a large shrinkage difference; Average wall thickness, balanced activity, and reduced injection pressure.
2. The product wall thickness is too thin or the activity is too long, resulting in difficult activity and excessive residual stress; Design thinking about formability (such as /T ratio)
1. The uneven wall thickness of the product results in abnormal activity in the thin area, and short shots in severe cases; Try to average the wall thickness when designing.
2. Unbalanced activity of each acupuncture point in the multi-mode acupuncture; Balance the runner design and use mold flow analysis to calculate its size.
3. The specifications of the injection line do not match; Measure the machine based on the product size.
4. Lack of plastic mobility; Adjust the temperature shot pressure to improve (refueling).
5. Short shots due to poor exhaust; Increase the exhaust slot and reduce the rate of fire.
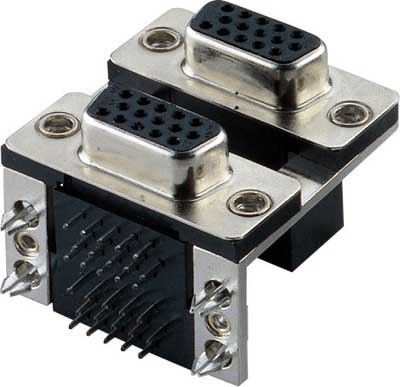
Ⅸ、Reasons for warping and deformation of the connector plastic shell:
1. The uneven wall thickness of the product results in a large shrinkage difference; Average wall thickness, balanced activity, and reduced injection pressure.
2. The product wall thickness is too thin or the activity is too long, resulting in difficult activity and excessive residual stress; Design thinking about formability (such as /T ratio)
3. Improper design of mold temperature cooling system, large temperature difference between male and female molds, and different shrinkage on both sides to form warpage; Cooling configuration design should, parameter control (temperature / flow rate).
4. The ejector position is not balanced. For products that are difficult to demold, they will deform after ejection; The ejection is balanced, and the thimble is added to the large holding area.
Ⅹ、Reasons for burrs formed by injection molding:
1. Improper product/mold design, resulting in excessive injection pressure. The clamping force of the machine is not enough, and the mold cannot be tightly formed to produce hair; Increase the meat thickness/average meat thickness, carefully choose the plastic/LT ratio, and improve the speed/low pressure and high speed.
2. The strength of the mold is not enough, it deforms during injection, the mold cannot be tightly closed, and the high temperature mold is prone to occur; Calculate the pressure to design the mold size. Increase the mold reinforcement design such as auxiliary columns, use low shrinkage and high strength steel.
3. Plastics have good mobility but slow solidification, and burrs can also be produced in small gaps; Higher requirements for mold accuracy, lower plastic mold temperature, lower molding injection pressure.