High-quality wiring harness used in autonomous vehicles

High-quality wiring harnesses are essential for car connection and autonomous driving. As the quality assurance is a complex and manually intensive manufacturing process is completed, and therefore the use of specialized manufacturing execution systems (MES) is essential.
Digital has long been an integral part of a modern vehicle technology aspects. From the engine control system to the driver assistance system to the media center, the entire car is full of information technology and continues to develop. With the rapid development of connected cars and autonomous vehicles, the peak of information technology is coming.
A core element of automotive IT is the wiring harness. It serves as the backbone for connecting digital components to each other or to other components (such as engines or chassis), and provides power for various devices.
The wiring harness has become the key to vehicle efficiency and safety. Malfunctions such as stereo systems can be annoying. Even the malfunction of the driver assistance system may be discovered by a careful driver. However, as self-driving cars become mainstream, failures of individual components or the wiring harness that connect them are intolerable. In this regard, quality requirements will also increase substantially. Broken wires or loose connections in the harness system can mean life and death. Therefore, all systems connected by wire harnesses must be designed for redundancy.
Not long ago, the wiring harness used for a certain model was the same for all vehicles of that model. Each type of wiring harness must include all possible selection models, regardless of whether the model is used by a vehicle. Some car manufacturers still manufacture wiring harnesses in this way. Other automobile manufacturers design and manufacture wiring harnesses, and only produce the wiring required for vehicle customization. On the one hand, because of the limited space of the vehicle, try to avoid using unnecessary wires. On the other hand, reduce the weight of the wires themselves. Automotive wiring harnesses are now not only very long, but also quite heavy, 50 to 60 kilograms (110 to 132 pounds) is quite common. Saving weight can reduce fuel consumption and harmful emissions. Therefore, more wiring harness systems need to be customized.
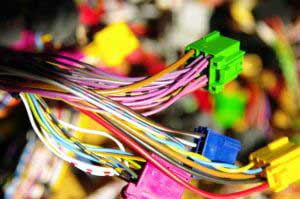
Production of automotive wiring harness
Major international automotive wiring harness manufacturers, such as Delphi, LEONI, and Yazaki, can provide the highest quality, very flexible and flexible small batch production. And will not reduce any quality requirements.
Not long ago, the wiring harness used for a certain model was the same for all vehicles of that model. Each type of wiring harness must include all possible selection models, regardless of whether the model is used by a vehicle. Some car manufacturers still manufacture wiring harnesses in this way. Other automobile manufacturers design and manufacture wiring harnesses, and only produce the wiring required for vehicle customization. On the one hand, because of the limited space of the vehicle, try to avoid using unnecessary wires. On the other hand, reduce the weight of the wires themselves. Automotive wiring harnesses are now not only very long, but also quite heavy, 50 to 60 kilograms (110 to 132 pounds) is quite common. Saving weight can reduce fuel consumption and harmful emissions. Therefore, more wiring harness systems need to be customized.
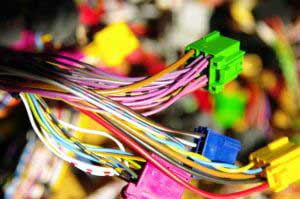
Production of automotive wiring harness
Major international automotive wiring harness manufacturers, such as Delphi, LEONI, and Yazaki, can provide the highest quality, very flexible and flexible small batch production. And will not reduce any quality requirements.
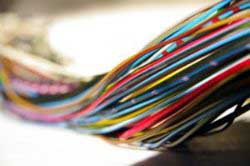
Phase 1: From design to production
This process starts with the design and development of the wiring harness. The car manufacturer provided the wiring harness manufacturer with 150% drawings of the vehicle wiring system design. This includes all possible wiring harnesses and possible choices made according to all models.
The engineers of the wire harness manufacturer use this drawing to create production drawings, work plans and corresponding parts lists. In addition, manufacturers regularly release schedule changes and must adjust their plans accordingly.
As always, when it comes to manual work, especially if these tasks must be performed under time pressure, the error rate can be high. In addition, the results of manual work depend on the individual's working methods, depending on which engineer is working, the production plan may look different. In addition, frequent changes to drawings are not always implemented in a timely manner.
Since all these aspects can compromise quality, it makes sense to use a software control planning system. In such a system, the manufacturer can use the blueprint to determine the rules of the production plan. For example, specify the steps that will be performed mechanically, these steps depend on different machines, and which production steps will be performed manually or semi-automatically. These rules must be flexible so that adjustments can be made. For example, they might look like this:
If single line, and size 0.35<cross section<6 mm², use standard machine
Based on these rules, the system interprets and analyzes the drawings of automakers and generates production data, including work plans and parts lists. In addition to greatly saving working time, due to the elimination of manual failure sources and the standardization of implementation procedures, the quality advantage is great.
This software can also calculate production documents based on specific on-time delivery schedules. In this way, a series of suitable wiring harnesses for vehicles will be delivered on time.
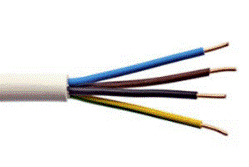
The second stage: production of automotive wiring harness
At the ERP level, the task of the Manufacturing Execution System (MES) is to control and record the production of automotive wiring harnesses. However, due to the many specific aspects of automotive wiring harness production, general MES systems cannot be used. For example, their IT technology related to wiring harnesses was unsuccessful.
Therefore, different wire harness manufacturers have developed their own MES systems. However, when the production process or ERP system changes, these customized software solutions are no longer applicable. Another problem is that know-how is often not clearly written in documents and is associated with specific employees. Therefore, leading automotive wire harness manufacturers rely on systems developed specifically for the wire harness industry.
Wire harness production is divided into three stages: wire cutting, pre-assembly and final assembly.
Stripping
Wire processing is highly automated in the field of wire stripping. The automatic machine first cuts the length of the wire cutter to the determined length, then strips the skin and lays the terminal. More complex machines can perform additional process steps, such as stranding. The wires produced in this way are grouped into bundles and can be used in the next production step.
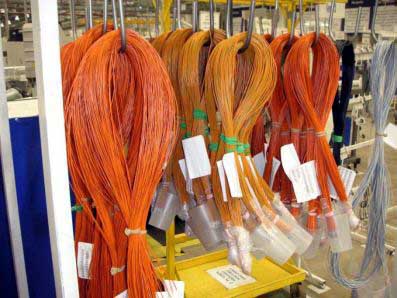
In order to increase productivity, a special MES system is used to ensure the optimal distribution of orders among different machines. But quality and traceability are important here. In CST machines, the productivity is usually high, and the wire is sometimes small in diameter. Of course, the CST machine itself is the main guarantee of accuracy and quality, but MES can also directly pass control data (such as curling data) to the machine. MES can also ensure quality assurance processes, such as scanning bar codes of wires and terminals, performing crimp height and tension tests, and monitoring the use and maintenance of tools. In order to establish traceability, MES assigns a unique ID to each harness produced and manages it throughout the process.
Pre-assembled
The next production stage of the wiring harness is manual. In the first pre-assembly stage, the wire harness produced in the stripping area is assembled into simple components, using things such as crimping, ultrasonic welding, and twisting. At the same time, a new ID will be generated, including all components.
As mentioned earlier, due to cost reasons, manufacturers often shift production to low-cost labor countries. The entire factory seemed to be built overnight, so thousands of new employees had to be recruited. However, lack of relevant experience and technical qualifications means a high risk of product quality. MES software company attaches great importance to direct guidance to employees in the workplace.
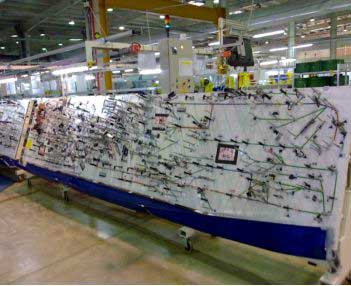
Final assembly
In the final assembly area, the wire harness is assembled on the wire harness board. Generally, the wire harness board is installed on a mobile assembly line, in which an assembler installs one or more wires to the wire harness board. At each workstation, each employee must perform the correct work steps. Since wire harnesses are usually produced according to the customer's specific conditions, the work steps may vary from wire harness to wire harness. Therefore, errors are likely to occur, which is an additional challenge for quality assurance. MES uses displays to control this complex process. The displays provide employees with detailed information about the relevant work steps to be performed. The system can also prompt employees to confirm certain steps, execute test steps or enter QA related data. Therefore, in these highly manual processes, the software can provide high quality.
Of course, the final assembly record is updated. The completed wiring harness is now composed of hundreds or thousands of components, and the system keeps a complete historical record for each component. The system tracks the machines, employees and tools in the production process of each wire harness.
This means that you can then determine which vehicle's wiring harnesses are made with a specific batch of wires. This also allows any repairs or recalls to be isolated, and any product liability issues can be quickly clarified.
In the increasingly digitalized automotive technology, the quality control of software management is critical to the production of automotive wiring harnesses. Otherwise, the demanding quality of this difficult task cannot be guaranteed. Traceability is the key to ensuring product quality and managing product recalls. The traditional MES system is not competent to manage the highly specialized task of automobile wiring harness production. The introduction of advanced management technology, software, AI, etc. into the production of automotive wiring harnesses will make quality assurance more reliable.