Injection Molds for Wire Harness Wrapping
The utility model relates to the technical field of injection molding of wire harnesses and connector inserts, in particular to an injection mold for covering multiple wire harnesses.

Background technique:
Metal insert injection molding is a type of insert model that pre-fixes the metal insert in the appropriate position in the mold, and then injects the plastic for molding. After the mold is opened, the inserts are wrapped tightly by the cooled and solidified plastic to form a method of covering wire harnesses and connectors with inserts such as threaded rings, electrodes, etc.
When multiple wire harnesses are injected as inserts, in order to fix and limit the multiple wire harnesses, a plurality of guide holes are usually provided on the top surface of the injection mold. Insert one end of each wire into the guide hole on the mold, and make the metal piece (insert) at the other end of the wire in the mold, and then perform injection molding. In order to prevent the plastic from flowing out, the guide hole on the mold should not be too large, and the guide hole that is too small will make the operation of the insertion process more difficult, time-consuming and labor-intensive, and low in efficiency. Therefore, how to provide a multi-wire harness injection mold with more convenient and efficient operation has become an urgent problem to be solved.
Technical implementation elements:
Therefore, the technical problem to be solved by the present invention is to overcome the defects of the injection mold in the prior art that it is difficult to operate and has low efficiency. Thus, a mold for multi-wire harness injection molding with more convenient and efficient operation is provided.
The utility model provides a mold for multi-wire harness injection molding. Including: a body, the body is an open structure.
The splicing part is arranged at the open structure of the main body, and the splicing part includes at least two splicable sub-parts, and is suitable for fixing the multi-wire harness.
In one embodiment, each of the sub-sections is provided with a wire-catching groove, and the wire-catching grooves on the two facing sub-sections are in one-to-one correspondence.
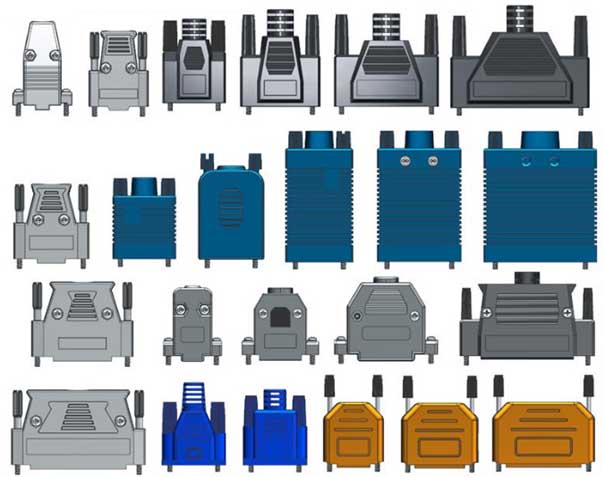
In yet another embodiment, a plurality of the wire clamping grooves are distributed along the length direction of each of the subsections at intervals, and the extension direction of each of the wire clamping grooves is consistent with the width direction of the subsections.
In yet another embodiment, the subsection has a first type of block and a second type of block; The first type of block is provided with a first plug on one side of the first type of block where the wire card slot is distributed; The second type of block is provided with a first jack on the side where the wire card slot is distributed; The first jack is pluggably connected to the first plug.
In yet another embodiment, the subsection has a first type of block and a third type of block; The first type of block is provided with a first plug on one side of the first type of block where the wire card slot is distributed; The third type block is distributed with the two opposite planes of the wire card slot, both of which are provided with second jacks; The second jack is pluggably connected to the first plug.
In yet another embodiment, the subsection has blocks of a first type, blocks of a second type, blocks of a third type, and blocks of a fifth type; The first type of block is provided with a first plug on one side of the first type of block where the wire card slot is distributed; The second type of block is provided with a first jack on the side where the wire card slot is distributed; The third type block is distributed with the two opposite planes of the wire card slot, both of which are provided with second jacks; The fifth type block is provided with a third plug on two opposite planes where the wire card slot is distributed; The first plug is pluggably connected to the second socket on one of the planes of the third type block; The second socket on the other plane of the third type block is pluggably connected to the third post on one plane of the fifth type block; The third plug on another plane of the fifth type block is pluggably connected to the first socket.

Background technique:
Metal insert injection molding is a type of insert model that pre-fixes the metal insert in the appropriate position in the mold, and then injects the plastic for molding. After the mold is opened, the inserts are wrapped tightly by the cooled and solidified plastic to form a method of covering wire harnesses and connectors with inserts such as threaded rings, electrodes, etc.
When multiple wire harnesses are injected as inserts, in order to fix and limit the multiple wire harnesses, a plurality of guide holes are usually provided on the top surface of the injection mold. Insert one end of each wire into the guide hole on the mold, and make the metal piece (insert) at the other end of the wire in the mold, and then perform injection molding. In order to prevent the plastic from flowing out, the guide hole on the mold should not be too large, and the guide hole that is too small will make the operation of the insertion process more difficult, time-consuming and labor-intensive, and low in efficiency. Therefore, how to provide a multi-wire harness injection mold with more convenient and efficient operation has become an urgent problem to be solved.
Technical implementation elements:
Therefore, the technical problem to be solved by the present invention is to overcome the defects of the injection mold in the prior art that it is difficult to operate and has low efficiency. Thus, a mold for multi-wire harness injection molding with more convenient and efficient operation is provided.
The utility model provides a mold for multi-wire harness injection molding. Including: a body, the body is an open structure.
The splicing part is arranged at the open structure of the main body, and the splicing part includes at least two splicable sub-parts, and is suitable for fixing the multi-wire harness.
In one embodiment, each of the sub-sections is provided with a wire-catching groove, and the wire-catching grooves on the two facing sub-sections are in one-to-one correspondence.
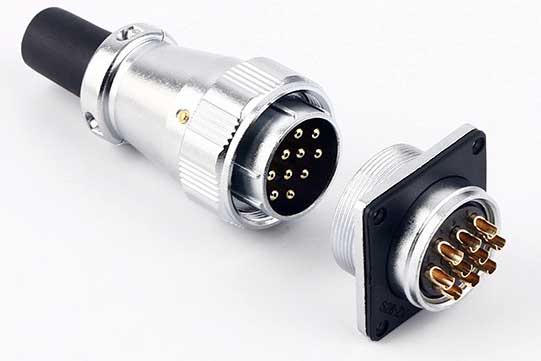
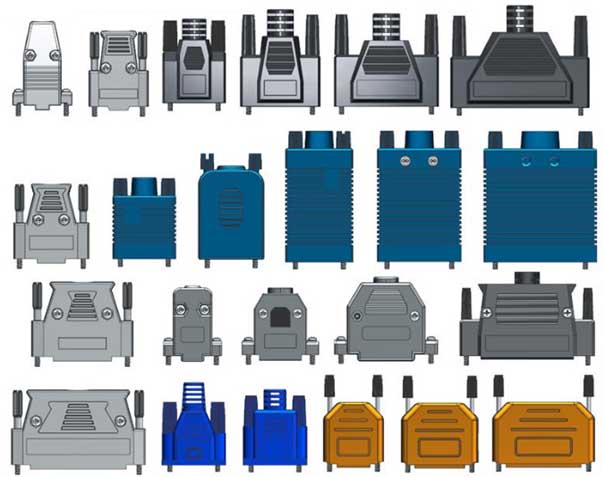
In yet another embodiment, a plurality of the wire clamping grooves are distributed along the length direction of each of the subsections at intervals, and the extension direction of each of the wire clamping grooves is consistent with the width direction of the subsections.
In yet another embodiment, the subsection has a first type of block and a second type of block; The first type of block is provided with a first plug on one side of the first type of block where the wire card slot is distributed; The second type of block is provided with a first jack on the side where the wire card slot is distributed; The first jack is pluggably connected to the first plug.
In yet another embodiment, the subsection has a first type of block and a third type of block; The first type of block is provided with a first plug on one side of the first type of block where the wire card slot is distributed; The third type block is distributed with the two opposite planes of the wire card slot, both of which are provided with second jacks; The second jack is pluggably connected to the first plug.
In yet another embodiment, the subsection has blocks of a first type, blocks of a second type, blocks of a third type, and blocks of a fifth type; The first type of block is provided with a first plug on one side of the first type of block where the wire card slot is distributed; The second type of block is provided with a first jack on the side where the wire card slot is distributed; The third type block is distributed with the two opposite planes of the wire card slot, both of which are provided with second jacks; The fifth type block is provided with a third plug on two opposite planes where the wire card slot is distributed; The first plug is pluggably connected to the second socket on one of the planes of the third type block; The second socket on the other plane of the third type block is pluggably connected to the third post on one plane of the fifth type block; The third plug on another plane of the fifth type block is pluggably connected to the first socket.
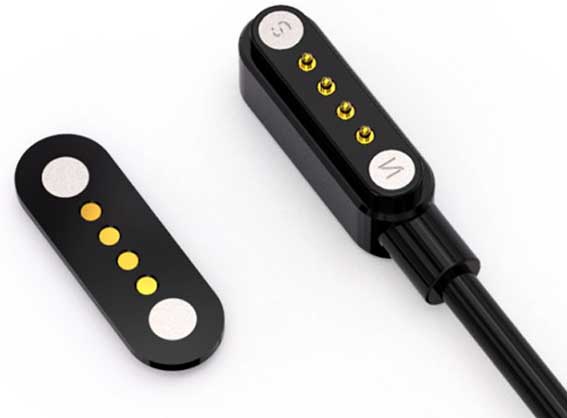
PREV:Advantages of Connector and Wire Harness Overmolding
NEXT:NONE
NEXT:NONE