China power cord manufacturer
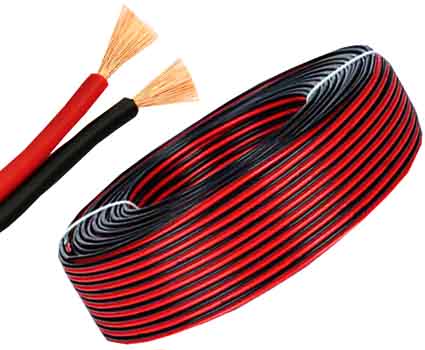
A power cord is a wire that transmits electric current. Usually the method of current transmission is point-to-point transmission. Power cords can be divided into AC power cords and DC DC power cords according to their usage. Generally, the AC power cord is a wire that passes high-voltage alternating current. Because of the high voltage, this kind of wire needs to obtain a unified standard to obtain safety certification before it can be officially produced. The DC line basically passes the direct current with a lower voltage, so the safety requirements are not as strict as the AC line, but for safety reasons, countries still require unified safety certification.
The structure of the power cord
The structure of the power cord is not very complicated. If you understand the power cord well, in some places you still need to understand the structure of the power cord professionally.
The structure of the power cord mainly includes an outer sheath, an inner sheath, and a conductor. Common transmission conductors include copper and aluminum metal wires.
Outer sheath
The outer sheath is also called the protective sheath, which is the outermost layer of the power cord. This outer sheath plays a role in protecting the power cord. The outer sheath has powerful characteristics, such as high temperature resistance, low temperature resistance, resistance to natural light interference, good winding performance, long service life, and environmental protection of materials.
Inner sheath
The inner sheath is also called an insulating sheath, which is an indispensable middle structure part of the power cord. As the name implies, the main function of the insulating sheath is insulation to ensure the safety of the power cord. Let the copper wire and the air not have any leakage phenomenon, and the material of the insulating sheath should be soft to ensure that it can be well inlaid in the middle layer.
Copper wire of power cord
The copper wire is the core part of the power cord. The copper wire is mainly the carrier of current and voltage. The density of the copper wire directly affects the quality of the power cord. The material of the power cord is also an important factor for quality control, and the quantity and flexibility of the copper wire are also one of the factors to be considered.
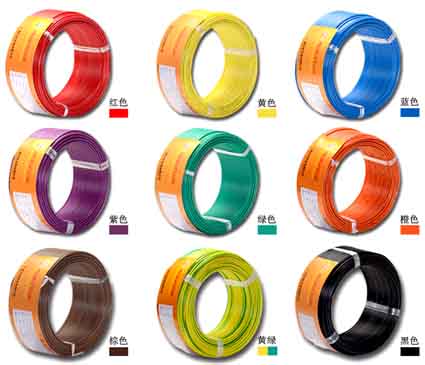
Inner sheath of power cord
The inner sheath is a layer of material that wraps the cable between the shielding layer and the core, usually polyvinyl chloride plastic or polyethylene plastic. There are also low-smoke and halogen-free materials. Use in accordance with the process regulations, so that the insulating layer will not come into contact with water, air or other objects, and avoid moisture and mechanical damage to the insulating layer.
The function of the power cord
Although the power cord is only an accessory for home appliances, it plays a vital role in the use of home appliances. If the power cord is broken, the entire appliance cannot be used. Household power cords should adopt BVV2×2.5 and BVV2×1.5 type wires. BVV is the national standard code and is a copper sheathed wire. 2×2.5 and 2×1.5 represent 2-core 2.5 square millimeters and 2-core 1.5 square millimeters, respectively. In general, 2×2.5 is used as the main line and trunk line, and 2×1.5 is used as a single electrical branch line and switch line. Single-phase air-conditioning dedicated line uses BVV2 × 4, and a dedicated ground wire is also provided.
Manufacturing process of power cord
Power cords are produced every day. Power cords need to be more than 500,000 meters and 50,000 plugs a day. With such huge data, the production process must be very stable and mature. After continuous exploration and research, it has been recognized by the European VDE certification body, the national standard CCC certification body, the American UL certification body, the British BS certification body, and the Australian SAA certification body. The power cord plug is mature, let’s introduce it below:
1. The power cord is drawn by copper and aluminum monofilament
At room temperature, use a wire drawing machine with copper and aluminum rods to pass through one or several stretch die holes to reduce the section, increase the length, and improve the strength. Wire drawing is the first process of various wire and cable companies, and the primary process parameter of wire drawing is mold matching technology.
2. Monofilament annealing of power cord
When the copper and aluminum monofilaments are heated to a certain temperature, the method of recrystallization is used to improve the toughness of the monofilament and reduce the strength of the monofilament to meet the requirements of the wire and cable for the conductive core. The key to the annealing process is to eradicate the oxidation of the copper wire.
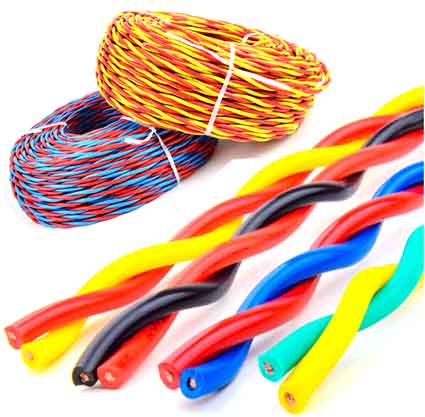
3. Stranding of power cord conductors
In order to improve the flexibility of the power cord and facilitate the installation of the device, the conductive core is formed by twisting multiple monofilaments. From the stranding method of the conductive core, it can be divided into regular stranding and irregular stranding. Irregular stranding is divided into bundle stranding, concentric stranding, extraordinary stranding and so on. In order to reduce the footprint of the wire, reducing the power supply line geometry, the stranded conductor is pressed embodiment also uses the popular variation semicircular circular, fan-shaped, W-shaped and pressed circular. This kind of conductor is mainly used on the power cord.
4. Extrusion of insulation layer of power cord
The plastic power cord adopts a squeezed solid insulation layer. The primary process requirements for plastic insulation extrusion:
1) Stretching degree: The deflection value of the extruded insulation thickness is the main indicator of the degree of extruding to work. The product structure size and its bias value have rules in the specification.
2) Lubricity: The surface of the extruded insulation layer must be lubricated, and it must not show poor quality problems such as rough appearance, scorching, and impurities
3) Density: The cross-section of the extruded insulation layer should be dense and firm, free of pinholes visible to the naked eye, and free of air bubbles.
5. The power cord is processed into a line
Regarding the multi-core power cord, in order to ensure the molding degree and reduce the shape of the power cord, it is generally required to twist it into a round shape. The mechanism of twisting is similar to that of conductor twisting, because the twisting pitch diameter is large, and most of the twist-free methods are used. Technical requirements for cable formation: One is to prevent the twisting of the cable due to the overturning of the special-shaped insulated core; The second is to avoid scratches on the insulating layer.
When the power cord is formed into a cable, there are two other processes: One is to fill to ensure that the cable is round and unchanged; One is lashing to ensure that the cable core is not loose.
6. The inner protective layer of the power cord
In order to protect the insulated core from being damaged by the armor, proper maintenance of the insulating layer is required. The inner protective layer is divided into: extruded inner protective layer (isolation sleeve) and wrapped inner protective layer (cushion layer). The wrapping buffer layer replaces the lashing tape and the cable forming process is carried out simultaneously.
7. Power cord armor
Laying in the underground power line, it can accept certain positive pressure effect during the task, and the inner steel tape armor structure can be selected. The power cord is laid in a place with both positive pressure effect and tensile effect (such as water, vertical shaft or soil with large drop), and the structural type with inner steel wire armor should be selected.
8. The outer sheath of the power cord
The outer sheath is the part of the structure that maintains the insulation layer of the power cord to avoid corrosion of the situation elements. The primary effect of the outer sheath is to improve the mechanical strength of the power cord, prevent chemical corrosion, moisture, waterproof, and prevent the power cord from burning. According to the different requirements of the power cord, the plastic sheath should be directly extruded by the extruder.