Flat wire and cable manufacturer
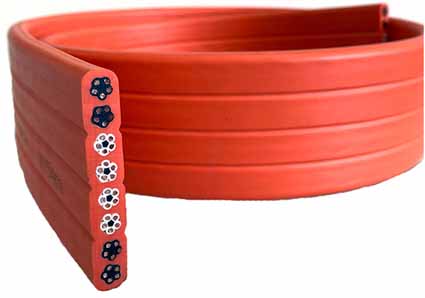
(YB, YBF, YBZ) Flat cables are produced by standard organizations and are suitable for mobile electrical equipment with AC rated voltages of 450V/70V and below. The flat structure is especially suitable for frequent bending occasions, no kinks, and neat folding. YB, YBF, YBZ three categories of products can meet the needs of various occasions. It is suitable for electrical connection between mobile electrical equipment in harsh environments such as power generation, metallurgy, chemical industry, and ports.
Technical requirements for flat cables
1. AC rated voltage:
Uo/U = 450V/750V;
Uo: the effective value of voltage between any phase conductor and ground;
U: The effective value of the voltage between any two-phase conductors.
2. Operating voltage:
In the AC system, the working voltage is not more than 1.1 times the rated voltage;
In the DC system, the working voltage is not more than 1.5 times the rated voltage.
3. Long-term working temperature of wire core: less than or equal to 65℃.
Uses of flat cables
1. Power core conductor;
2. Insulation;
3. Adhesive tape;
4. Ground wire core conductor;
5. Insulation;
6. Filling layer;
7. Control core conductor;
8. Insulation;
9. Sheath.
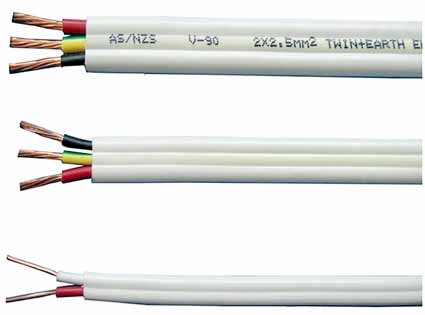
Technical parameters of flat cable
1. When the insulation resistance of the flat cable is converted to a length of 1km and the temperature is 20℃, the power core should not be less than 30MΩ/km.
2. For the voltage test of the flat cable, the power cores should be able to withstand the 50Hz, 2500V voltage test for 5 minutes, and control
The wire cores should be able to withstand the AC 50Hz, 1500V voltage test.
3. The delivery length of the flat cable should not be less than 150m, and the short cable length is not less than 35m to be delivered. The delivery quantity should not exceed 10% of the total delivery length. According to the agreement between the user and the manufacturer, any length of cable is allowed to be delivered.
Flat cable forming method
As a multi-core cable, flat cables were first used in electronic computers and electronic instruments. Because of its flexibility and small wiring space, it has also been widely used in civilian electrical appliances such as telephones and tape recorders. In order to meet different requirements, some new flat cables are constantly being developed. The application of the insulation displacement connector makes the termination of the flat cable extremely convenient and reliable. At the same time, higher requirements are put forward for the geometrical dimensions of the flat cable center distance tolerance, center distance cumulative error, and insulation thickness, which makes the manufacture of flat cables more difficult.
The production process of flat cables is basically similar to that of plastic wiring. In the flat cable forming unit, in addition to adding a flat cable forming device related to the main process of insulating material processing. Multi-head pay-off racks, cooling water tanks, spark detectors, tractors and coil forming machines are basically similar to those used in plastic wiring production.
The flat cable molding method is to sandwich a group of core wires evenly arranged at a certain interval between two plastic films, and bond the three to form a flat cable by certain means. There are two problems to be solved during molding, one is how to produce two layers of plastic film that can be bonded or fused to each other, and the other is to ensure that a group of wires are always kept at a certain distance and arranged evenly.
The insulation of flat cables includes soft polyvinyl chloride, polyester and fluoroplastics. The processing properties of these polymer compounds are different, and different processing methods must be used to make them shaped. People have developed a variety of flat cable forming machines. Although each has its own characteristics, they can basically be divided into four categories.
1. Direct extrusion method. Use plastic extruder to directly extrude flat cable with die, such as flat cable machine of KABLEMETAL company in West Germany and flat cable machine of MAILFLER company in Switzerland.
2. Laminating method. The wire and plastic are pressed into a cable through a pair of rollers. This method can be divided into two types according to the source of the plastic film. A method called extruded film lamination, such as the flat cable machine of Japan Showa Wire and Cable Co., Ltd.;
The other is called prefabricated film lamination, such as the ribbon cable machine of the 23rd Research Institute of the Ministry of Mechanical and Electrical Engineering.
3. Bonding method. The two pieces of film and the wire are bonded and formed by an adhesive, such as the polycool flat cable machine of No 20 factory above.
4. The method between the two molding methods, such as the shielded flat cable machine combined with the extrusion method and the lamination method, has been reported in many documents.
Flat cable production requirements
Various flat cable forming methods have their scope of application and advantages and disadvantages. Which molding method is used in production depends on the processing performance of the insulating material. There are two types of molding methods for flat cables of some specifications. For example, UL2651 can adopt direct extrusion method or lamination method; And some flat cables can only use one molding method, such as UL2468 and UL2877 can only use the direct extrusion method, and UL2902 can only use the bonding method. Various UL standard flat cable forming methods are clearly stipulated in the UL file.