Models and characteristics of drag chain cables
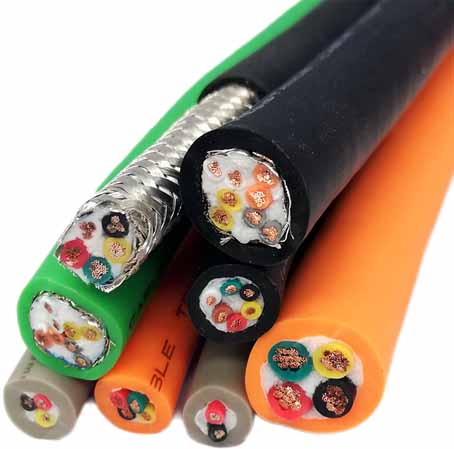
Conventional model of drag chain cable
TRVV: copper core nitrile PVC insulated, nitrile PVC sheathed drag chain cable.
TRVVP: copper core nitrile PVC insulated, nitrile PVC sheath, soft sheath tinned copper wire mesh braided shielded drag chain cable.
TRVVSP: copper core nitrile polyvinyl chloride insulated, nitrile polyvinyl chloride sheathed twisted overall shielded drag chain cable.
RVVYP: Copper core nitrile mixed special insulation, nitrile mixed special sheath oil-resistant general-shielded drag chain cable.
Conductor: multiple strands of ultra-fine finely stranded oxygen-free copper wire with a diameter of 0.1 ± 0.004 mm. If you have special requirements, you can choose other types of copper wires according to the customer's technical indicators.
Insulation: special mixed nitrile polyvinyl chloride material insulation.
Color: According to the customer's specification.
Shield: Tinned copper wire mesh weave density above 85%
Sheath: Mixed nitrile polyvinyl chloride special bending resistant, oil resistant, abrasion resistant, waterproof jacket.
There are many types of drag chain cables, the number of cores ranges from single core to 60 cores, and the area of single core covers all models ranging from 0.08 to 60.
3×4mm 3×6mm 3×10mm 3×35mm 3×50mm 3×70mm 3×150mm
3×4+2×1mm 3×6+2×1mm 3×6+2×1.5mm 6×2.5+6×1.5mm
3×4+4×2.5mm 3×25+1×10mm 3×16+1×10mm 3×35+1×10mm
3×50+1×10mm 3×16+1×10mm 3×10+1×6mm 3×4+1×2.5mm
There are some smaller than 1 square: for example, 6*0.75, 5*0.5, 5*0.2, etc. small square drag chain cable
Drag chain cable commonly known as: TRVV TRVVP TRVVSP and other national standard models
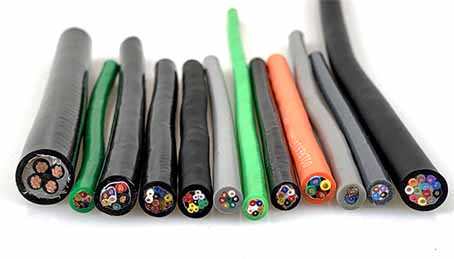
Application of drag chain cable
Drag chain cables are mainly used in:
Industrial electronic systems, automatic generation lines, storage equipment, robots, fire fighting systems, cranes, CNC machine tools and metallurgical industries.
General requirements for drag chain cables
1. The laying of towline cables must not be twisted. That is, the cable cannot be unwound from one end of the cable drum or cable reel. Instead, rotate the reel or cable reel to unwind the cable, and unwind or hang the cable if necessary. The cable used for this occasion can only be obtained directly from the cable roll.
2. Pay attention to the minimum bending radius of the cable. (The relevant information can be found in the flexible drag chain cable selection table).
3. The cables must be laid loosely side by side in the drag chain, separated as much as possible, separated by spacers or penetrated into the separation cavity of the bracket. The gap between the cables in the drag chain should be at least 10% of the cable diameter.
4. The cables in the drag chain must not touch each other or be trapped together.
5. Both points of the cable must be fixed, or at least at the moving end of the drag chain. Generally, the distance between the moving point of the cable and the end of the drag chain should be 20-30 times the diameter of the cable.
6. Please make sure that the cable moves completely within the bending radius, that is, it cannot be forced to move. In this way, the cables can be moved relative to each other or the guiding device. After a period of operation, it is best to check the position of the cable. This inspection must be performed after the push-pull movement.
7. If the drag chain breaks, the cable also needs to be replaced, because damage caused by excessive stretching cannot be avoided.